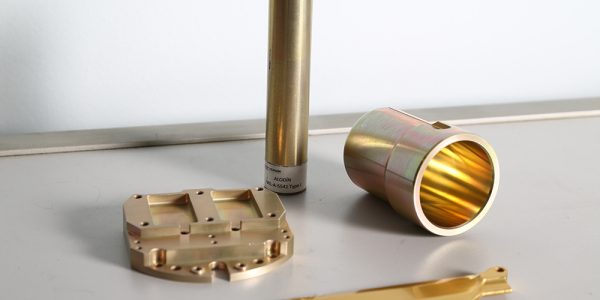
Aluminum Chromate Coating
Aluminum Chromate Coating process is creating a thin surface over aluminum and aluminum alloys to increase corrosion resistance, keep electrical conductivity, increase adhesion over surfaces to be painted and to add a decorative look.
Details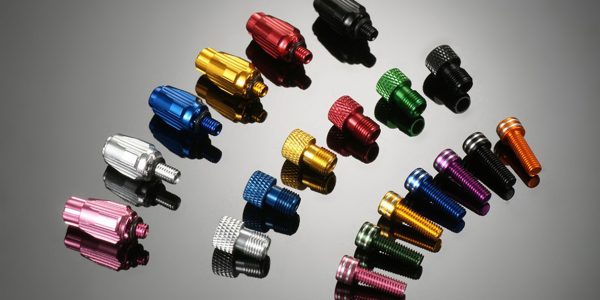
Anodized Coating
Meaning of anodized coating in word sense is oxidation of aluminum by using and electrolytic method. This process is also called as Anodic Oxidation or Anodization as well.
Details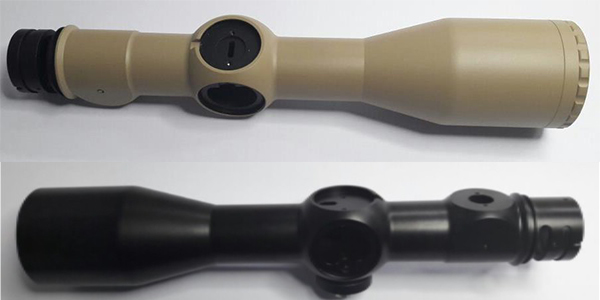
Cerakote Coating
Cerakote coating is ceramic based and is a type of coating similar to paint.
Details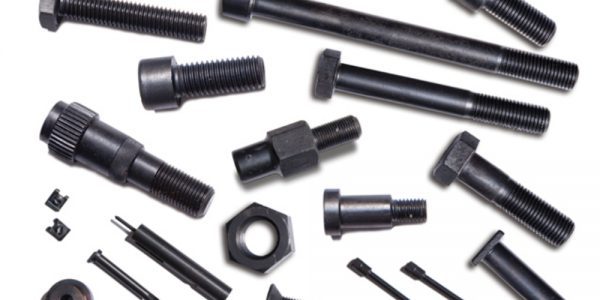
Chemical Blacking
This coating is a chemical black oxide coating of iron and iron alloy metals (wrought iron, low alloy steel and stainless steel).
Details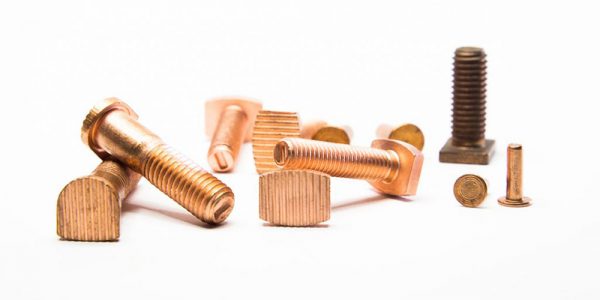
Copper Electroplating
Copper electroplating is usually applied for prime coat or base coat. This process increases the resistance against corrosion and also adds an extra gloss to the final coat.
Details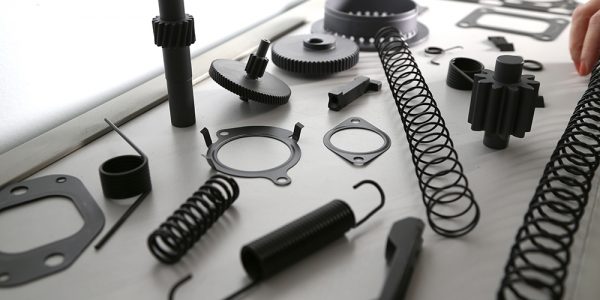
Dry Film Lubricant Coating (Technocoat ®)
Dry / solid film lubricant coating provides long-term protection, prevent damaging base metal by lubrication and sliding surfaces continuously and also protects from corrosion at the same time.
Details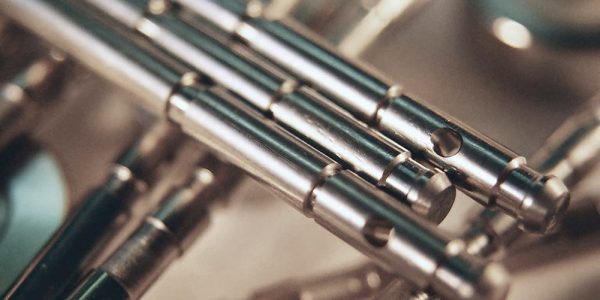
Electroless Nickel Plating
Electroless Nickel Plating is based on coating the metal and composite surfaces by Nickel-Phosphorus alloy.
Details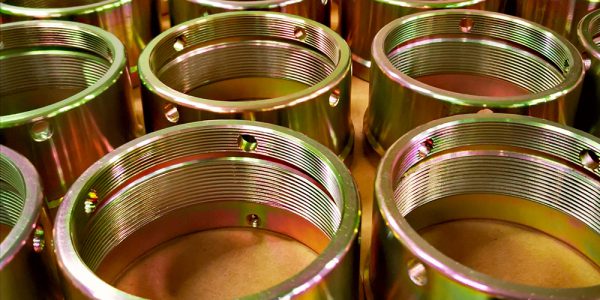
Electrolytic Zinc
Zinc Coating is applying a thin zinc coating over iron and steel parts. It is mainly preferred due to its cost and easiness.
Details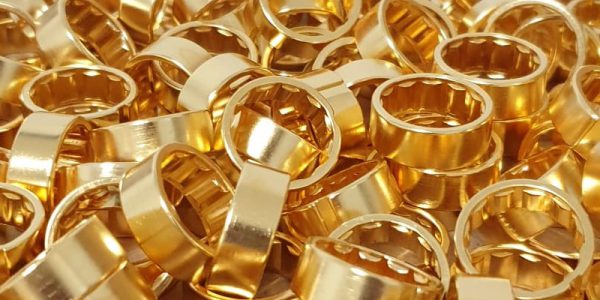
Gold Plating
Electrolytic Gold plating; steel, aluminum and alloys, zinc and alloys with nickel and alloys can be made on the hard, wear-resistant and bright yellow appearance is an acid-type electroplating
Details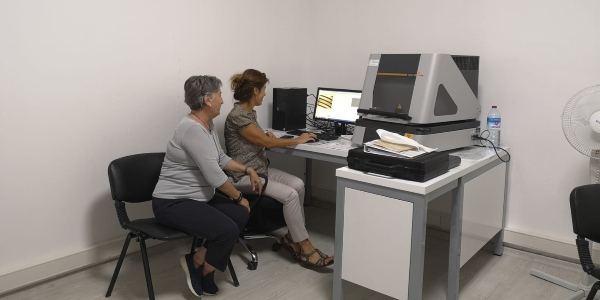
Laboratory Testing Services
Our laboratory is NADCAP accredited and the Tests in our Laboratory activities are served as a service to companies operating in the Defense and Aerospace Sector.
Details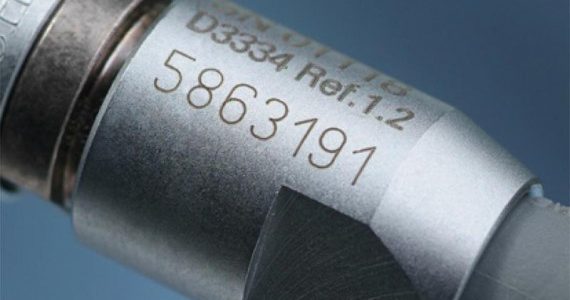
Laser Marking
Laser Marking is a non-contact printing method that offers advantages such as brand quality, durability and less consumption material.
Details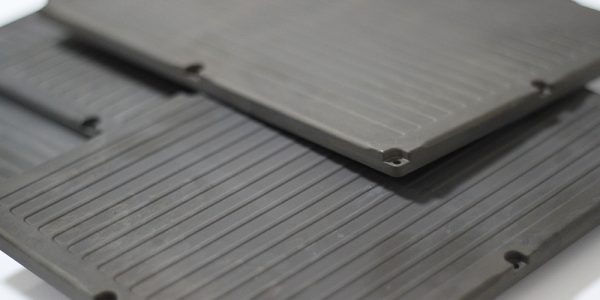
Magnesium Chromat Coating
Magnesium Chromate Coating treatment is increasing corrosion resistance by creating a film layer over alloy surfaces and increasing the adhesion ability on the surfaces to be painted.
Details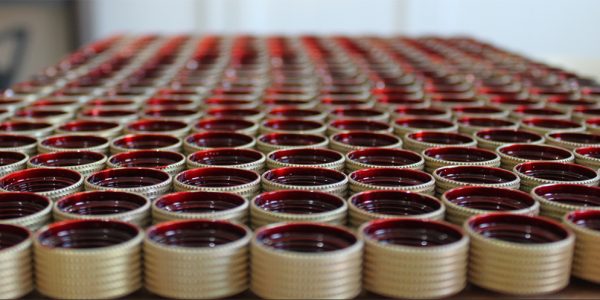
Masking
Towards the customer needs we also provide masking with maskant for the areas of the part which doesn’t want to be painted. Sometimes it needs to be masked two times due to three processes. We show great care on masking and removing the mask from the preserved area.
Details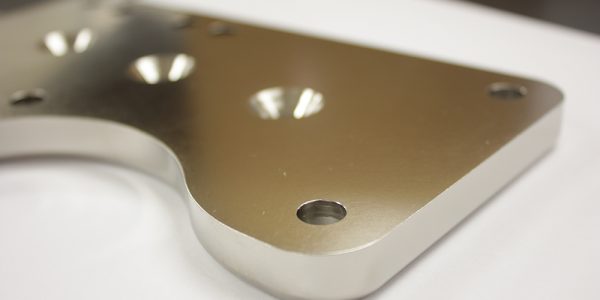
Nickel Electroplating
Nickel electroplating is based on electroplating the steel, copper and copper alloys, zinc and zinc alloys with nickel.
Details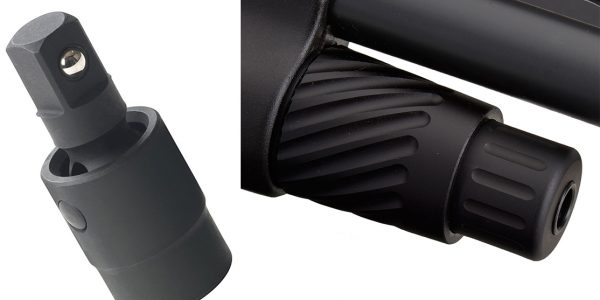
Phosphate Coating
Insulating and protective layer created by phosphate crystals over the steel surfaces is done via Phosphate Coating.
Details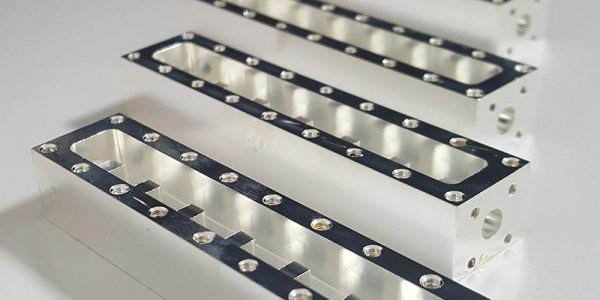
Silver Plating
Electrolytic silver-plated steel, copper and alloys, zinc and alloys, nickel and alloys can be made on a conductive, wear-resistant electroplating.
Details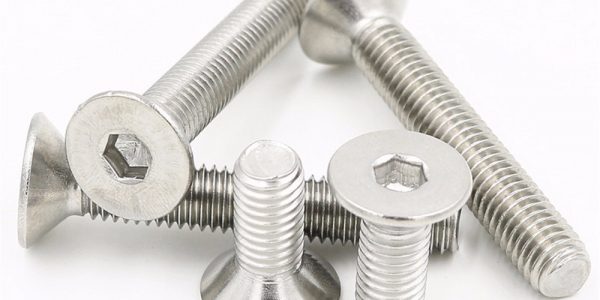
Stainless Steel Passivation
Purpose of this type of coating is cleaning the surfaces of corrosion resistant steels, removing the oxide layer from surface and creating a film layer which passives the surface.
Details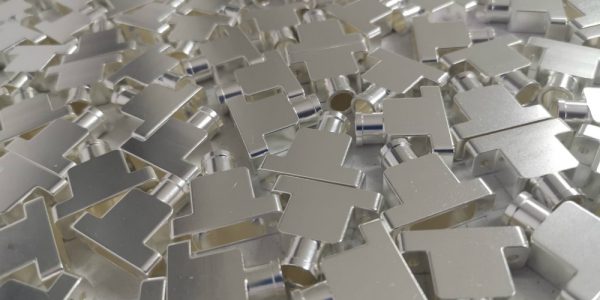
Tin Electroplating
Tin Electroplating is coating a thin tin surface to a metal surface by electroplating method.
Details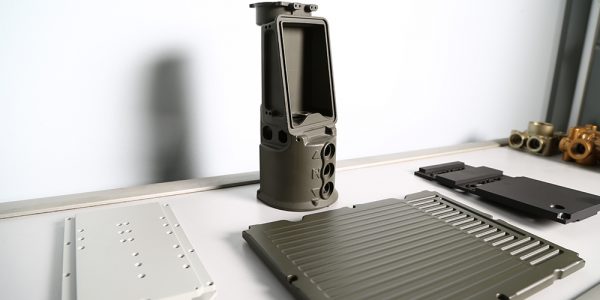
Wet Painting
It is applied to all metal surfaces to increase corrosion resistance and add a decorative appearance. It is based on applying solvent based epoxy, acrylic, polyurethane, infrared reflective paint and water-based paint by spraying.
Details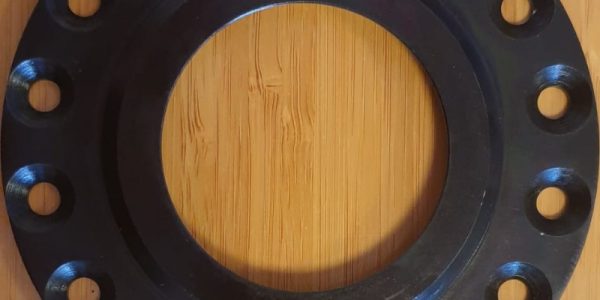
Zinc-Nickel Coating
Zinc-nickel coatings are normally used where conventional zinc plating is insufficient due to high temperatures or aggressive environmental conditions.
Details